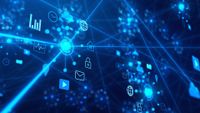
Everything you need to know about the Product Security and Telecommunications Infrastructure Act
Explainer Coming into force on April 29th, the Product Security and Telecommunications Infrastructure Act aims to tighten up manufacturer security and protect users