The best 3D printer tools and accessories for your business
Every business using 3D printers should be aware of these essential extras to raise its output to the next level
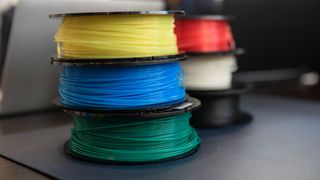
3D printers have a range of uses within a business, whether it’s for printing custom circuit boards, scalable prototypes, or precision-moulded parts for a larger machine. Innovative companies have
Whether you’re making the step up to getting your business’ first 3D printer, or simply looking to further invest in the technology, there are a number of tools and accessories that can make your 3D printing experience that much better, regardless of the particular 3D printing use case.
Filament storage container
As anyone who has had the misfortune of having to deal with a 3D printer jam knows, it’s really important that moisture and dirt is kept away from filament as much as possible. Wet filament loses its structural integrity, and will not stick together properly in the printing process.
To that end, there are a range of filament storage containers available, to suit any size and filament type. Although a tightly-shut box could suffice to keep dust out, in wetter climates such as the UK it might not prevent moisture from getting to the filament held within.
This is where containers with desiccant inside come in. A desiccant is any compound that absorbs large amounts of moisture from the air, and they are often packed with products to absorb unwanted moisture. The most common day-to-day example of a desiccant is silica gel, which is often found in packets inside shoe boxes to keep moisture from compromising the quality of the shoes.
Desiccants can work wonders to keep filament dry, but after time will need to themselves be dried out or replaced altogether. Alternatives to using desiccants within filament containers include vacuum-sealed containers, which can efficiently keep filament in pristine condition, or vacuum packets into which conventional containers can be sequestered.
Filament dryers
If you are unable to keep your filament dry, it can be salvaged by being precisely dried. This is where filament dryers come in, offering consistent temperature and humidity control and specifically built with filament in mind.
Get the ITPro. daily newsletter
Receive our latest news, industry updates, featured resources and more. Sign up today to receive our FREE report on AI cyber crime & security - newly updated for 2024.
The more premium filament dryers even have screens that show users temperature readings, and allow for settings to be tweaked to suit exact drying needs.
Digital Calliper
A digital calliper can take the accuracy of your measurements to a new level, providing accurate measurements for every occasion on a handy digital display.
Businesses that invest in a digital calliper can forget having to awkwardly mark a ruler to transfer measurements from one print to the next, with the most accurate models offering readings accurate to three decimal places.
Good quality print beds
A house is only as stable as the foundation that it's built on, and a 3D print is no different. Investing in a good quality print bed can elevate the sturdiness and accuracy of your prints,
Good thermal resistance is a must, as print beds can be heated to 90-110°C during the printing process. Heated beds help to ensure that the first layer of the print remains stable, to prevent the entire structure from sticking to the nozzle and potentially tearing itself apart as the print continues.
Print remover
Even the best quality print materials cannot totally guarantee that prints won’t become fused to the print bed once complete, and in these circumstances it’s important to have a print remover available.
Also known as ‘hot bed shovels’ or ‘spatulas’, print removers are essentially a sharp, flat blade that lets a user scrape their print from the bed without risking damage to the finished product. If you don’t fancy ordering a custom tool online, any good hardware shop will have a scraper/spackle knife in stock, also known as a putty knife. Although these are intended for plastering jobs, they work just the same as a print remover and are even available in larger sizes to suit your needs.
Range of nozzles
Nozzle attachments free you from the confines of your default nozzle width, allowing you to fill larger builds quicker or alternatively achieve a level of detail impossible with larger filament. This could be especially useful for businesses 3D printing custom tools, or even printing custom circuit boards.
Conductive filament
On the previous point, if your business is looking to 3D print circuit boards, 3D printers can go a step further than just setting out a blank board with holes for the conductive element.
Conductive filament can be used to lay down a predefined board pattern, and is made of materials such as carbon fibre and graphene. It’s important to note that 3D printed filament can only take quite a low voltage, so proposed builds must always take into account the manufacturer-defined limits to avoid damage or safety hazards.
Companies offering conductive filament include Protopasta, NinjaTek and Voxelab.
Nozzle cleaning tools
Needles make for ideal nozzle-cleaners, as the sharp and thin tips can get into the nozzle to clear away any excess filament that might be causing problems or even blocking the nozzle entirely.
For best results, it's recommended that you heat the nozzle to melt the excess filament as much as possible, allowing it to be easily scraped away with the sharp tip of the needle.
Specialist cleaning kits are available, with a range of needle sizes and proper grips to prevent unnecessarily fiddly cleaning jobs or even minor injury.
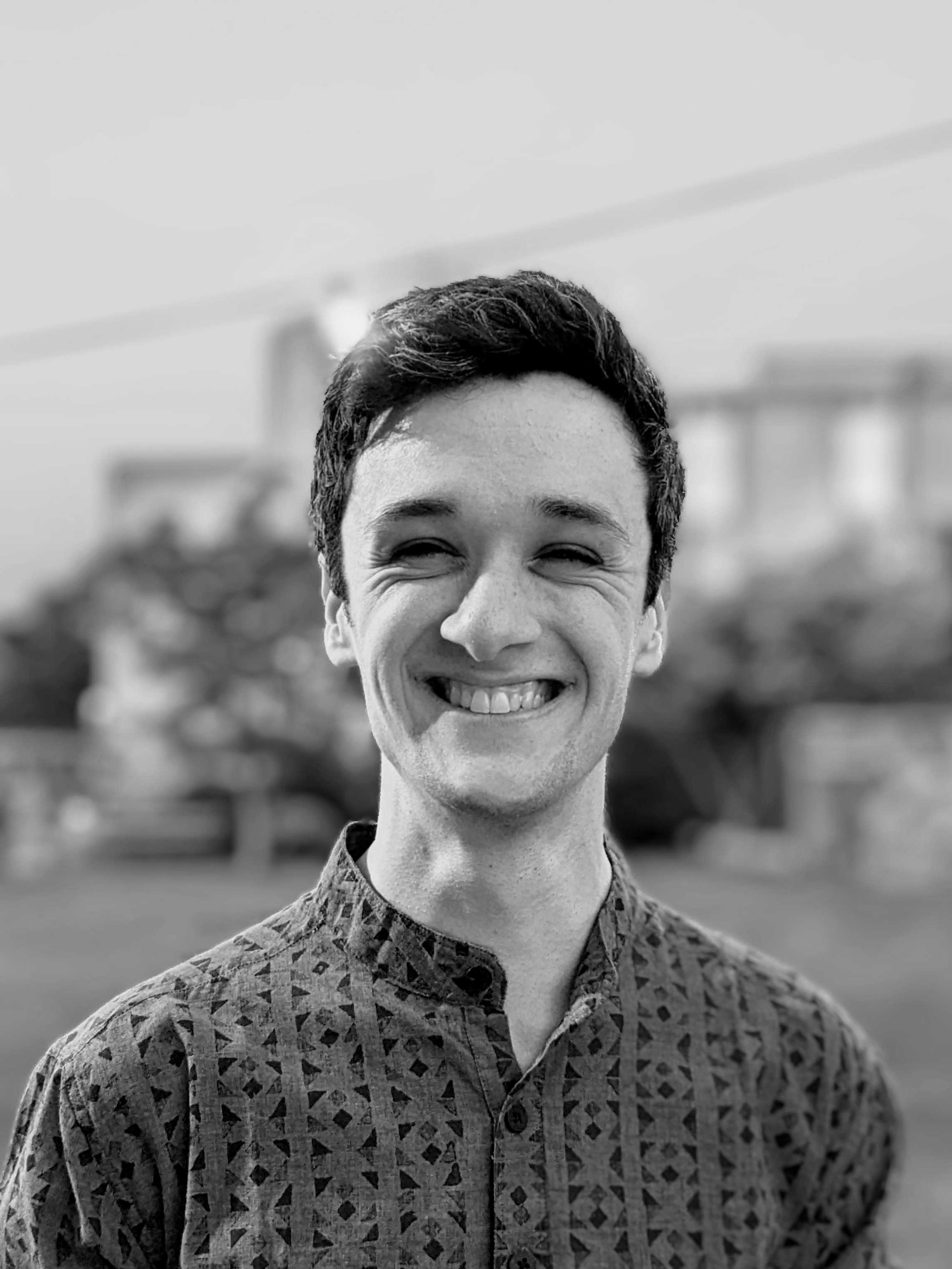
Rory Bathgate is Features and Multimedia Editor at ITPro, overseeing all in-depth content and case studies. He can also be found co-hosting the ITPro Podcast with Jane McCallion, swapping a keyboard for a microphone to discuss the latest learnings with thought leaders from across the tech sector.
In his free time, Rory enjoys photography, video editing, and good science fiction. After graduating from the University of Kent with a BA in English and American Literature, Rory undertook an MA in Eighteenth-Century Studies at King’s College London. He joined ITPro in 2022 as a graduate, following four years in student journalism. You can contact Rory at rory.bathgate@futurenet.com or on LinkedIn.